先頭構体は、まず、先端部、屋根、窓枠、側面などのブロック毎に分けて製作され、完成した各ブロックを溶接で接合します。
- ① 部材切り出し
標準定型サイズのアルミ板から、シャーリング(せん断)やレーザー切断で部品を切り出します。
- ② 簡易プレスならびに成形加工機による成形
この段階で大まかな曲げを施します。
- ③ ハンドハンマー手作業による微調整
鉄のかたまりの台のうえでハンマー手作業で金属板を叩いて微調整を行います。金属板を骨組にあてがって精度を確認しながら進めます。叩きと確認を何度も繰り返し、骨組にぴたりと合うまで仕上げます。
- ④ 接合(TIG溶接等)と歪の除去
打ち出し成形された複数の板を溶接で接合し、再びハンドハンマーで溶接歪みを取ってブロックができあがります。
車両外板には高い信頼性が求められます。作業に際しては、見て、触って、音を聞いて、研ぎ澄まされた感性が総動員されます。
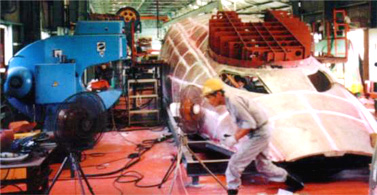
JR西日本500系新幹線先頭構体製作風景(1995年9月撮影) 写真は、500系新幹線先頭構体の製作風景です。
1995年に製作の量産先行車用1構体をはじめ(もう1つの量産先行車用構体は川崎重工業殿で製造されました)、1997年から1998年にかけて合計9つの先頭構体を製作(シェア50%)。
500系新幹線のベースになった高速試験車両WIN350先頭構体も同じ場所で製作されました。
運転室となる部分には円形冶具を使用、また、前照灯となる部分(向かって左側)には、構体の内側から手槌を片手に歪みを補整中の技能者の姿が見えます。
製造の現場では、部材の仕上がりに合わせ、様々な機械、冶工具から手槌一本まで、最適な加工手段が選ばれ、各々の備え持つ特性が技能者により最高度に引き出されながら、ものづくりに活かされています。